SKF Lüchow: Ein Meilenstein in der Produktionsautomatisierung
In einer herausragenden Kooperation haben SKF und rbc robotics im SKF Werk Lüchow neue Maßstäbe in der Automatisierung der Produktion gesetzt. Durch die Einführung von 29 hochindustrialisierten Roboterzellen, die rund um die Uhr im Einsatz sind, sowie einem fortschrittlichen Fertigungskonzept, das auf „Individualität durch Modularisierung“ setzt, konnte nicht nur die Produktionseffizienz erheblich gesteigert, sondern auch die gesteckten Produktionsziele übertroffen werden.
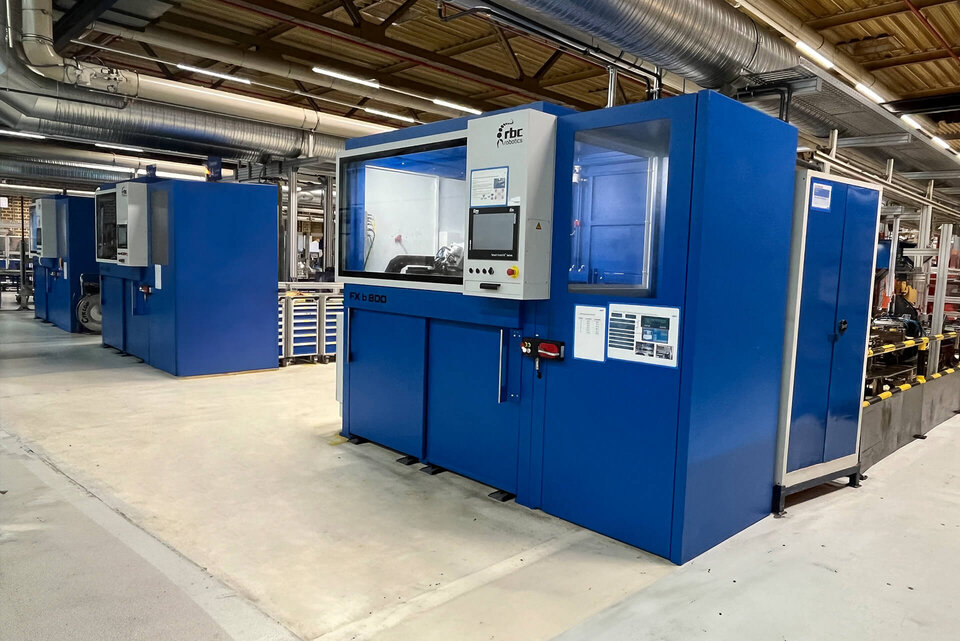
Unser Kunde
SKF in Lüchow ist ein herausragendes Beispiel für Innovation und Effizienz in der modernen Fertigungstechnologie. Als Teil der global agierenden SKF Gruppe, die sich auf die Entwicklung, Produktion und den Vertrieb von Wälzlagern und Dichtungen spezialisiert hat, zeichnet sich der Standort Lüchow durch seine fortschrittlichen Produktionsverfahren und die Implementierung von zukunftsweisenden Technologien aus. Der Erfolg von SKF in Lüchow basiert auf einer Kombination aus technologischer Expertise, kontinuierlicher Innovation und dem Engagement für Qualitätsstandards, was diesen Standort zu einem Vorbild in der Branche und einem Schlüsselakteur innerhalb der SKF Gruppe macht.
Revolutionäre Automatisierung auf kleinem Raum
Das Herzstück dieses Fortschritts ist die hochmoderne Automatisierungstechnologie von rbc robotics, die es ermöglicht, maximale Leistung auf minimaler Fläche zu erbringen. Durch die Einführung eines modularen Anlagenkonzepts konnten zwei Zellentypen entwickelt werden, die eine erhebliche Optimierung der Produktionslinien erlauben. Jede Zelle der insgesamt 29 Roboterzellen, ausgestattet mit einem Industrieroboter und einer integrierten siebten Linearachse, steigert die Effizienz im 24/7 Betrieb durch kontinuierliche Materialzufuhr und Palettierung.
Herausforderungen und innovative Lösungen
Die Herausforderung lag in der Steigerung des Autonomiegrades, insbesondere in der automatisierten Zuführung und Verpackung der fertig produzierten Ringe. Trotz räumlicher Beschränkungen und der Notwendigkeit, ein breites Spektrum an Ringgeometrien zu bewältigen, ermöglichte die modulare Lösung eine effiziente Umsetzung innerhalb des vorgegebenen Zeit- und Budgetrahmens. Die Zuführung der Ringe, die direkt aus der Härterei ungeordnet in Behältern ankommen, erfolgt über einen sehr dynamischen Binpickingroboter mit Pickraten von ca. 10 Bauteilen pro Minute. Es wurden dabei überragende Ergebnisse erzielt, was den Entleerungsgrad der Behälter, den Typenwechsel (bis 40 Varianten pro Channel) und die Zuverlässigkeit des Gesamtsystems anbelangt. Am Ende der Produktionslinie werden die Ringe ebenfalls automatisch auf Zwischenlagen verpackt. Das erfolgt mit dem gleichen Basismodul der modularisierten Zelle und mit noch schnelleren Pickraten. Ein Teachen der Roboter ist hierbei Geschichte. Ebenfalls Schlagstellen und Bauteilbeschädigungen.
Ergebnisse, die überzeugen
Die Ergebnisse sprechen für sich: eine kontinuierliche 24/7 Zufuhr und Verpackung der Bauteile, die Stillstände vermeidet, eine spürbare Reduzierung des Schallpegels und eine Verringerung der körperlichen Belastung für die Mitarbeiter. Die Automatisierung hat es ermöglicht, dass sich die Mitarbeiter fast vollständig auf Qualitätssicherung und Fertigungsprozesse konzentrieren können. Zudem sind die Umrüstzeiten der Automationszellen bemerkenswert kurz, was eine flexible und leistungsstarke Produktion sicherstellt.
Eine Partnerschaft, die Maßstäbe setzt
Die Kooperation zwischen SKF und rbc robotics illustriert die Kraft effektiver Zusammenarbeit in der Automatisierungstechnik. Durch die Kombination aus technologischer Expertise und gemeinsamen Zielsetzungen konnten signifikante Fortschritte in der Produktionseffizienz und -technologie erzielt werden. Das Projekt ist ein klares Beispiel dafür, wie innovative Lösungen und starke Partnerschaften die Zukunft der Fertigungsindustrie prägen können.
Automation nach Maß: Möchten Sie mehr Fallbeispiele für individuelle Automatisierungslösungen von rbc robotics entdecken? Besuchen Sie den Bereich Smart Flex auf der Website von rbc robotics.
Wie zufrieden ist unser Kunde SKF zur diesem Projekt? Erfahren Sie es in unserem Interview mit Helge Koopermann, Projektleiter und Prozessingenieur bei SKF:
1. Wie würden Sie die aktuelle Zusammenarbeit zwischen SKF und rbc robotics beschreiben?
Herr Koopmann: Die Zusammenarbeit zeichnet sich durch eine gute Kommunikation, eine gemeinsame Zielverfolgung und eine vertrauensvolle Kooperation aus.
2. Welche Faktoren sind Ihnen bei der Auswahl eines Koopertionspartners besonders wichtig?
Herr Koopmann: Ehrliche und vertrauensvoll Kommunikation auf Augenhöhe. Glaubwürdigkeit der Umsetzung einer technischen Lösung.
3. Welche Herausforderungen sind in der Zusammenarbeit mit rbc robotics aufgetreten, und wie wurden sie bewältigt?
Herr Koopmann: Eine Herausforderung lag in der ambitionierten Zeitplanung des Projektes. Von Auftragsvergabe im Januar, bis zur Lieferung der ersten Maschine im Juli, sind lediglich 6 Monate vergangen. Auch bei den Folgelieferungen und den entsprechenden Installationen der Roboterzellen hat rbc robotics die Zugesagten Liefertermine eingehalten, sodass wir im Schnitt ca. alle 2-3 Wochen eine neue Roboterzelle in der Produktion integrieren konnten. Eine weitere Herausforderung war die modulare Konzipierung der Roboterzelle, die sowohl für rbc robotics als auch für SKF viele Vorteile mit sich gebracht hat. So konnten aus SKF-Sicht zum Beispiel eine schnelle Inbetriebnahme der Zelle sichergestellt werden. Ich erinnere mich gerne an ein Best-Case-Szenario, in dem wir es geschafft haben, dass eine Roboterzelle an einem Freitagvormittag per LKW angeliefert worden ist und diese bereits am darauffolgenden Sonntag zum Beginn der Nachtschicht um 22.00 Uhr der Produktion vollumfänglich zur Verfügung stand.
4. Wie profitiert SKF von der technologischen Expertise von rbc robotics?
Herr Koopmann: Bei der Umsetzung des benannten Projektes kam es mit Anwendung des Bin Pickings zum Einsatz einer marktneuen Technologie und den damit verbunden Herausforderungen. Die professionelle Vorgehensweise von rbc robotics bei der Durchführung eines Benchmarkings und der anschließenden Auswahl, sowie die Transparenz bezüglich des Ergebnisses der SKF gegenüber, war zu unserer vollen Zufriedenheit.
5. Wie sehen Sie die zukünftige Entwicklung der Zusammenarbeit zwischen SKF und rbc robotics? Gibt es geplante Projekte, die in naher Zukunft umgesetzt werden sollen?
Herr Koopmann: Einer zukünftigen Zusammenarbeit zwischen SKF und rbc robotics steht aus SKF-Sicht nichts im Wege. Es wurde bereits über eine weitere Automatisierung mit dem Umfang von 5 Roboterzellen im Bereich der Warmbehandlung gesprochen.