Wie eine smarte Front of Line auch komplexe Rohteilzuführung intelligent löst.
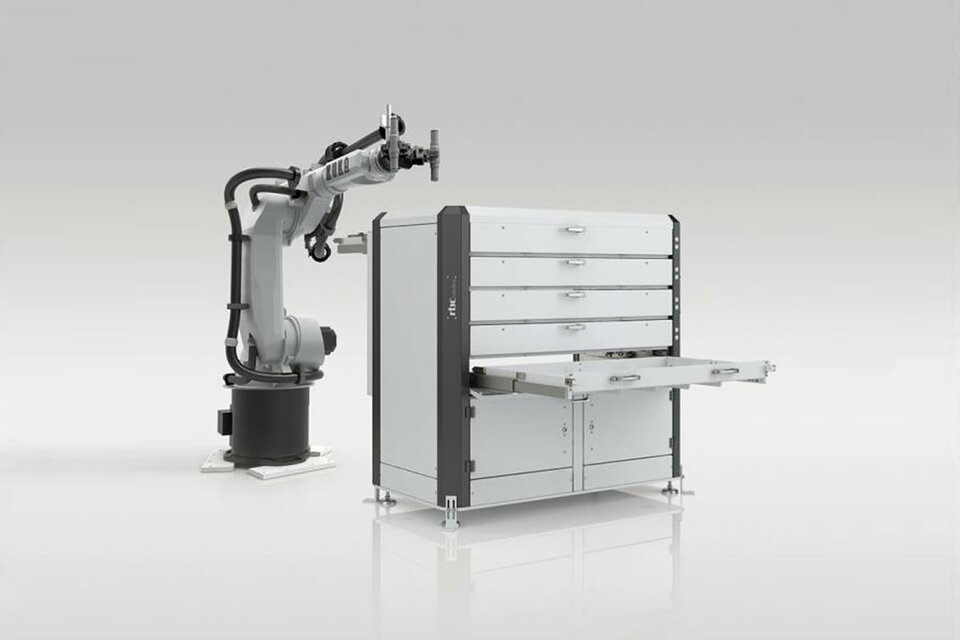
In klassischen Bearbeitungslinien werden Rohteile auch heute oft noch manuell zugeführt, was natürlich die Produktivität der Fertigungslinie beeinträchtigt. Durch diverse Behältergeometrien, in welche die Bauteile aus dem Vorprozess gelangen, gibt es oftmals keine definierte Bauteillage und somit auch keine hinreichenden automatisierungsgerechten Bedingungen.
Darüber hinaus ist bei hohen Werkstückgewichten der Einsatz von Hebezeugen erforderlich. Um also einen kontinuierlichen Nachschub an Rohteilen zu gewährleisten, ist hoher personeller Aufwand nötig. Diesen Herausforderungen hat sich die rbc Fördertechnik GmbH aus Bad Camberg gestellt und ein roboterbasiertes System entwickelt für die Zuführung von kartesisch angeordneten rotationssymmetrischen oder kubischen, auch sehr schweren Werkstücken. Mit diesem können Paletten oder Behälter automatisch ausgeräumt werden. Zusammen mit einem reduzierten und offenen Anlagenkonzept entsteht eine Lösung mit hohem Kundennutzen.
Das Herzstück der Anwendung ist ein 3D-basiertes Erkennungssystem, das stets die aktuelle Lage der Bauteile im Behälter ermittelt. Weil die Rohteilentnahme smart erfolgt, wird ein hohes Maß an Automationssicherheit erzielt. Der Roboter führt vor jedem Griff in die Kiste einen Szenescan durch. Die aktuelle Behältersituation ist die Ausgangslage für den nächsten Roboterzugriff. Bauteil und Behälter erfordern verschiedenste Ausräumstrategien, die eine vollständige und sichere Entnahme gewährleisten. Zum Beispiel befinden sich oftmals noch Transportsicherungen im Behälter, die vom Bediener im Vorfeld entnommen werden müssen. Das Vorhandensein dieser Transportsicherungen wird vom System sicher erkannt und gemeldet. Störungen werden auf diese Weise vermieden. Auch die Methodik der Bauteilentnahme aus dem Behälter erfolgt nach bestimmten Kriterien. So werden z.B. Bauteile mit Lage am Kistenrand anders abgegriffen, als Bauteile, die sich in der Mitte des Behälters befinden.
Das Erkennungssystem ist stationär oder robotergeführt, das heißt, der Sensor, welcher für die Detektion der Bauteile zuständig ist, wird im sicheren Abstand über den Behälter geführt. Bei Verwendung des präferierten Sensors liefert der Scan unter vorhandenen Umgebungsbedingungen der Fertigung und ohne Erfordernis zusätzlicher Fremdlichtabschottungen, äußerst stabile und zuverlässige Daten.
Adaptierbare Sensorik
Abhängig von der Beladesituation der Maschine und weiteren Anforderungen, kann das Erkennungssystem anwenderspezifisch zusammengestellt werden. Bei Ringen mit einem Gewicht von rund 20 kg beispielweise, werden Toleranzen von bis zu +/- 2 mm ohne Einbußen an die Automationssicherheit akzeptiert. Dieser Wert kann bei kleineren und komplexeren Geometrien nicht mehr hinreichend genau sein. In diesem Fall wird mit geänderter Sensorik und geringerem Scanabstand gearbeitet. Im Wesentlichen wird das Lasertriangulations- oder das Lichtlaufzeitmessverfahren angewendet. Bei der Lasertriangulation wird eine Laserlichtlinie ausgesendet und mittels integrierten Empfängers wieder aufgenommen. Der traversierte Sensor liefert dabei 3D-Punkteinformationen. Dabei spielt die Oberflächenbeschaffenheit des Bauteils eine entscheidende Rolle. Hohe Reflexion bei glänzenden Oberflächen führen dann bekanntlich zu schlechten Erkennungsraten bis hin zum Versagen der Anwendung.
Sehr gute Ergebnisse werden mit dem Lichtlaufzeitmessverfahren für die Objekterkennung und Abstandsmessung erzielt. Es wird hierbei ein Laserpuls mit aufmodulierter Frequenz verwendet. Dieser liefert die stabilsten, jedoch etwas unpräziseren Daten, die für viele Anwendungen jedoch noch hinreichend genau sind.
Der entsprechende Sensor wird in einem Abstand von ca. 40 mm bis ca. 2.500 mm über das Objekt geführt. Je nach Auflösung der Sensorik und Abstand zum Objekt erzielt man Genauigkeiten von bis zu 0,1mm. Die Sensorsignale werden aufgezeichnet und mit der entsprechenden Bewegungsrichtung und Geschwindigkeit kombiniert. Das Ergebnis des Objektscans ist eine Punktewolke. Das Recording der Punktewolke ist das Preprocessing in der Applikation. Hierbei spielt zunächst der eingesetzte Sensor die entscheidende Rolle. Durch die stetige Weiterentwicklung der Sensoren der Hersteller, sind in den letzten Jahren bedeutende Fortschritte erzielt worden, was die Leistungsfähigkeit und auch die Baugröße anbelangt.
Die Auswertung der Scandaten nach der Detektion (Postprocessing) erfolgt mittels einer PC-basierten Software. Beim angewendeten System erfolgt die Auswertung der Daten bauteilspezifisch. Das beutet, dass die Punktewolke nach einem definierten Algorithmus auf Linien oder Kreise ausgewertet wird, was sehr robuste und sichere Ergebnisse liefert. Die Gesamtgeometrie des Bauteils spielt bei dieser Art der Auswertung nicht immer die entscheidende Rolle. So ist es z.B. möglich, partielle Merkmale zu scannen und nur diese auszuwerten. Die restlichen Bauteilinformationen sind dann nicht relevant und die Applikation bedient sich nur mit den minimalen Scandaten. Das hat enorme Vorteile bezüglich der Datenerfassung und auf die Auswertezeiten. Die Auswertezeiten liegen bei den üblichen Anwendungen bei ca. einer Sekunde. Weiterer Vorteil des Systems ist, dass mehrere Sensoren mit einem PC ausgewertet werden können. Beispielsweise kann zunächst die Bauteillage im Behälter erfasst werden und anschließend partiell ein Geometriebereich zur zusätzlichen Prüfung eines Merkmals.
Darüber hinaus ist der 3D Scanner inkl. Auswerte-PC optimal in das Gesamtsteuerungskonzept integriert und bietet umfangreiche Diagnosemöglichkeiten. Ein Livebild des aktuellen Scans, umschaltbare Sprachen der Bedienerdialoge und der Fernzugriff sind dabei obligatorisch.
Der Industrieroboter mit meist pneumatischem Greifer ist somit in der Lage, mehrere bereitgestellte Paletten zu scannen und leer zu räumen. Die Bauteile liegen auf den Paletten grob vororientiert und in verschiedenen Ebenen ohne oder mit Zwischenlagen. Gerade die sichere Detektion eines Bauteilstapels (Z-Lage) zeichnet das System aus.
Die Umrüstung auf andere Bauteile erfolgt auf Knopfdruck, wenn das Greifsystem mit den verschiedenen Bauteilgeometrien arbeiten kann. Bei Ringen z.B. ist dies optimal zu realisieren, da dies eine einfache Bauteilgeometrie darstellt.
Nach der Entnahme des Werkstücks von der Palette oder aus dem Behälter, belädt der Roboter die erste Operation der Bearbeitungslinie, und sichert einen kontinuierlichen Teilefluss. Der Einfluss der Bediener an dieser wichtigen Schnittstelle der Anlage wird somit minimiert und beschränkt sich auf die Logistik der Behälterzuführung und -abführung.