Innenverzahnte Hohlräder sind wesentliche Antriebskomponenten, um effiziente E-Mobilität zu ermöglichen. Eigens für solche Bauteile wurde jüngst bei der DVS Production GmbH im thüringischen Krauthausen eine neue Produktionshalle gebaut.
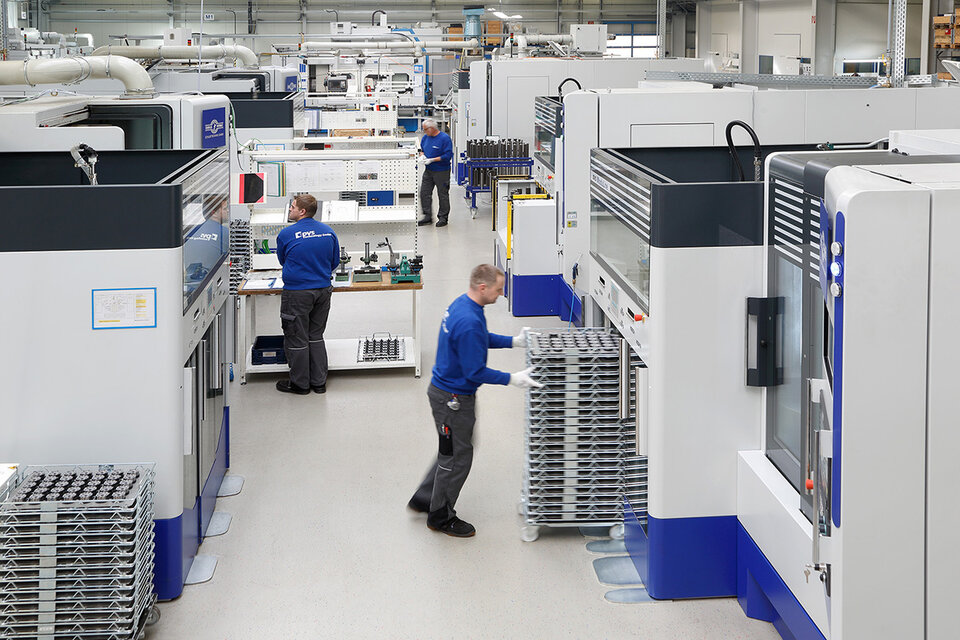
Für die Herstellung von Antriebskomponenten im Auftrag eines Tier-1 Lieferanten der Automobilindustrie hat die DVS Production GmbH im thüringischen Krauthausen eine neue Produktionshalle gebaut. Die dort gefertigten Hohlräder werden in Plug-in Hybrid und rein elektrisch betriebenen Fahrzeugen eingesetzt. Entsprechend hoch sind die Genauigkeitsanforderungen der Endkunden. Gemeinsam mit den DVS-Schwesterfirmen aus Maschinen- und Werkzeugbau entstand eine hochproduktive Fertigungslinie. Zerspanungstechnologien von PITTLER und PRÄWEMA, Werkzeuge von DVS Tooling und Spannmittel der SWS Spannwerkzeuge GmbH bilden das Fundament für die Produktion der anspruchsvollen Präzisionsbauteile.
Kurz bevor der Frost die Erde gefrieren ließ, rollten Ende 2017 die ersten Bagger auf das Gelände der DVS Production GmbH und begannen mit den massiven Erdbewegungen, die nötig waren, um das Fundament der neuen Halle auf gleichem Bodenniveau wie die bestehenden Produktionshallen zu errichten. „Etwa 80.000 Kubikmeter Erde wurden für die neue Halle bewegt“ berichtet Rainer Eisel, der seit Gründung des Unternehmens vor fast 15 Jahren die Geschäftsführung innehat. „Für den Bau der Halle und das Hochfahren der Fertigung blieb uns nur wenig Zeit. Der Kunde benötigte schnellstmöglich Teile.“ ergänzt Eisel. Tatsächlich wurde die neue 4.000 m² große Halle in einer Rekordzeit von nur 8 Monaten gebaut und an die bestehenden Hallen angedockt.
Fertigung nur mit DVS-Maschinen
Gefertigt werden in der neuen Halle sogenannte Hohlräder. Die innenverzahnten Bauteile sind Bestandteil des Planetengetriebes, welches dank seiner kompakten Bauweise, seines hohen Wirkungsgrades und seiner geräuscharmen Laufeigenschaften immer öfter in elektrischen Antrieben verbaut wird. „DVS Production ist bei diesem Projekt Lieferant zentraler Bauteile“, erklärt Mario Möller, ebenfalls Geschäftsführer und verantwortlich für den Bereich Produktion. Auch bei der Prozessauslegung sind die Ingenieure von DVS Production mit von der Partie. Sie besprechen mit den Kunden, wie das Bauteil beschaffen sein muss, um eine hocheffiziente Zerspanung zu ermöglichen. Dabei entdecken sie immer wieder versteckte „cost driver“, die sich in der frühen Phase der Prozessauslegung noch problemlos abstellen lassen.
Die geschmiedeten Ringe, aus denen später die Hohlräder gefertigt werden, müssen sich im Labor der neuen Halle zunächst einer Überprüfung der Eingangsqualität unterziehen. Nach dem ersten Zerspanungsprozess, der Drehbearbeitung, werden die Hohlräder sowohl am Innen- als auch am Außendurchmesser verzahnt. Da die aus Einsatz- oder Nitrierstahl gefertigten Hohlräder im Werk des Kunden in das Getriebegehäuse eingepresst werden, ist passend hierfür an der Außenkontur eine Blockverzahnung herzustellen. An der inneren Kontur soll eine Laufverzahnung mit hoher Oberflächenqualität eingebracht werden. Beste Voraussetzungen also, um die komplette Grünbearbeitung auf der neu entwickelten Maschinenplattform PITTLER SkiveLine zu erledigen.
Verbunden mit der multifunktionalen Automationszelle PAC (PITTLER Automation Center) operieren zwei SkiveLine-Verzahnungszentren als OP10 für die Außenbearbeitung und als OP20 für die Bearbeitung der Innenkontur. Lesen Sie mehr über die Bearbeitung der Hohlräder mit der PITTLER SkiveLine auf Seite 20 dieser DVSpezial Ausgabe.
Die anschließende Wärmebehandlung im Nitrierverfahren erfolgt bei einem externen Dienstleister. Das Verfahren hat bekanntermaßen den Vorteil, dass die Kernfestigkeit des Werkstückmaterials hochgehalten werden kann. So können die Aufmaße für das Verzahnungshonen wesentlich geringer gehalten werden, was sich positiv auf die Taktzeit und auf die Kosten pro Bauteil niederschlägt. Auf ein üblicherweise nachfolgendes Plan- und Außenrundschleifen der Bauteile kann somit verzichtet werden.
Hohe Drehzahlen in E-Antrieben erfordern Hartfeinbearbeitung
Vor ein paar Jahren wäre das Bauteil nach dem Härten fertig zum Kunden gegangen. Höhere Drehzahlen in Elektromotoren, einhergehend mit höheren Traganteilen an den Zahnflanken, machen es jedoch erforderlich, das Bauteil nach dem Härten hartfein zu bearbeiten. Im letzten zerspanenden Bearbeitungsschritt wird aus diesem Grund die Innenverzahnung auf einer PRÄWEMA SynchroForm V Maschine gehont. Mit anderen Worten, die Oberflächenqualität der Verzahnung wird deutlich optimiert. Pro Flanke werden etwa 50 µm Material abgetragen. In einem prozesssicheren Verfahren entsteht so die hohe Verzahnungsqualität 8, wodurch akustische Auffälligkeiten im Getriebe fast gänzlich vermieden werden.
Nach dem Innenverzahnungshonen wird auf jedes Bauteil ein DMC-Code gelasert. Loggt der Kunde sich später auf den Datenaustauschserver von DVS Production ein und scannt den Bauteil-Code, kann er beispielsweise die bei der nachfolgenden 100%igen Qualitätskontrolle erstellten Messprotokolle abrufen. Auch das Herstelldatum mit Zeitangabe oder die Seriennummer des Bauteils lassen sich gleichermaßen abrufen.
Durchlaufzeiten weiter verkürzt
Bevor die Bauteile schließlich den Weg zum Kunden antreten, werden sie in den letzten Arbeitsschritten noch gewaschen, konserviert und verpackt. „Mit dem Bau der neuen Halle haben wir unsere innerbetrieblichen Logistikprozesse überarbeitet und konnten unsere Durchlaufzeiten weiter verkürzen“, ergänzt Möller.
Unterm Strich wurde mit der neuen Fertigungslinie ein weiteres erfolgreiches Zukunftsprojekt realisiert. Neben Antriebswellen, Sonnen- und Planetenrädern fertigt man nun auch Hohlräder für Elektro- und Hybridfahrzeuge in Serie. Zudem konnten 30 neue Arbeitsplätze geschaffen werden. „Das nächste Projekt steht schon in den Startlöchern“, verrät Rainer Eisel.